Analysis
We carry out plating solution analysis and plating film property analysis for the aim of maintaining and improving plating quality. Importance is placed on the enrichment of analysis equipment and developing personnel with accurate knowledge when managing environmentally hazardous substances including RoHS Directive and REACH Regulations as well as analysis of property data to verify processes enabling a trustworthy system which puts our customers’ minds at ease.
Plating film analysis
Items of analysis | Equipment | |
Monitoring, component analysis | ・Monitoring plating particles ・Monitoring adhered foreign materials ・Monitoring plating structure with cross section sample |
Scanning electron microscope (SEM) |
---|---|---|
・Component analysis of adhered foreign materials ・Analysis of plating structure with cross section sample |
Energy dispersive X-ray spectrometer (EDS) | |
・Component analysis of adhered foreign materials | Fourier transform infrared spectrophotometer (FT-IR) | |
・Enlarged imaging | Digital microscope | |
Film thickness measurement | ・Measuring plate film thickness | Fluorescent X-ray analysis device |
Roughness | ・Measuring surface roughness | Laser microscope |
measurement | ・Measuring and determining surface unevenness depth | Roughness measurement device |
Melting point measurement | ・Measuring melting point | Melting point measurement device |
Hardness measurement | ・Measuring hardness | Vickers hardness meter |
Electrical properties | ・Measuring electrical resistance | Electric contact point simulator |
Resistance gauge | ||
Soldering properties | ・Measuring solder wettability | Solder checker |
・Measuring adhesion | Digital force gauge | |
Other | ・Cross section polishing machine | Cross section polisher |
Tabletop precision polishing machine |
Plating film reliability testing
Items of analysis | Equipment | |
Environment testing | ・Environmental testing with constant temperature and humidity | Thermo‐hygrostat |
---|---|---|
・Environmental testing with changing temperature | Temperature cycle testing machine | |
・Environmental testing under constant temperature, humidity and pressurized environment | Pressure cooker testing device | |
・Corrosion testing | Salt water spraying testing device |
Plating solution analysis
Items of analysis | Equipment | |
Concentration measurement | ・Measuring concentration level of solution | Sequential ICP atomic emission spectrometry analyzer |
---|---|---|
Ultraviolet and visible spectrophotometer | ||
Potential difference automatic titrator |
Equipment utilization example ①
Scanning electron microscope- Energy dispersive X-ray analyzer (SEM-EDS) + Cross section polisher
Case 1: Evaluating plating film reliability (Cu materials-Ni plating-Sn plating thermal diffusion)
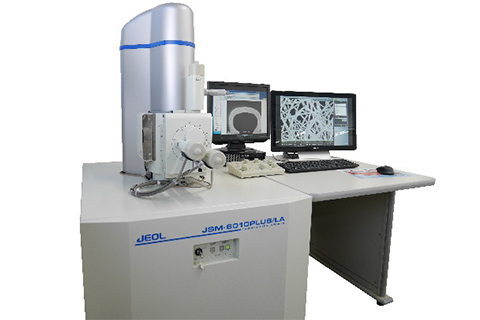
Analysis involves Ni-Sn plating samples on Cu materials heated for a long time, and the diffusion state of Cu, Ni and Sn before and after was observed using a scanning electron microscope (SEM) and energy dispersive X-ray spectrometer (EDS).
In addition to observing the surface with the SEM, a cross section sample was made with a cross section polisher and diffusion state was investigated through observation in the same manner.
Surface and cross section observation with scanning electron microscope
スクロールでご覧になれます。
Surface | Cross section | |
Before heat testing | ![]() |
![]() |
After heat testing | ![]() |
![]() |
Element distribution observation of compounds using the energy dispersive X-ray analyzer
スクロールでご覧になれます。
Sn | Ni | Cu | |
Before heat testing | ![]() |
![]() |
![]() |
After heat testing | ![]() |
![]() |
![]() |
As a result of element distribution observation of the cross-section sample with EDS, mainly Ni-Sn was diffused to form the compound.
Case 2: Monitoring substances adhering to the surface
We received a request to investigate a whisker like material. Analysis was carried out on the surface.
Surface observation
Adhered substance | Whiskers (as reference) |
![]() |
![]() |
Cross section observation
Cross section observation with SEM | Element distribution observation with EDS | |
Sn | Cu | |
![]() |
![]() |
![]() |
When observing the cross section, tin plating particles can be confirmed. Further observation of element distribution showed copper in the center and it turned out that this was not a whisker but tin plating formed on material burr.
Equipment utilization example ②: Digital microscope + laser microscope
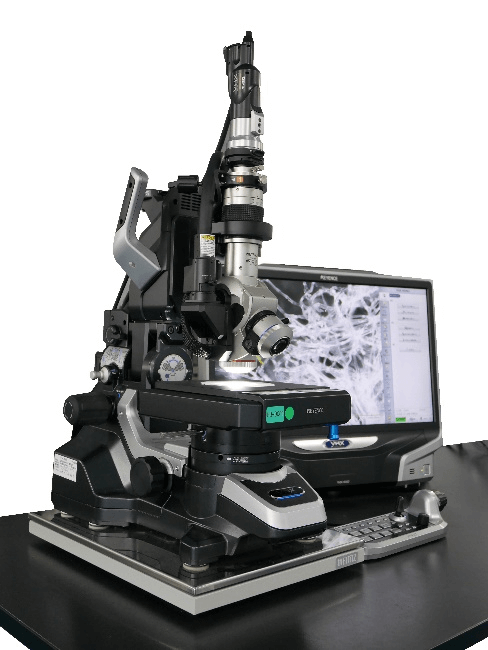
Digital microscope
We observed and measured irregularities on the sample surface using a digital microscope with the capabilities of confirming the surface condition in a wide range and visually recognizing the shape and a laser microscope capable of measuring the shape of the unevenness.
Surface conditions are identified in 3D using a digital microscope.
Enlarged surface image
Enlarged image | 3D composite image | |
![]() |
![]() |
![]() |
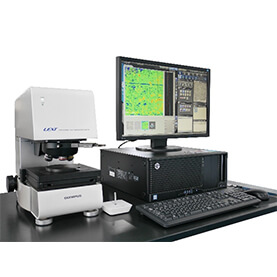
Next, the surface was observed and measured in detail using a laser microscope.
Surface observation and measurement images
Brightness | Tone | Cross section profile of surface |
![]() |
![]() |
![]() |
The enlarged image and cross section profile show protrusions in the convex edge with a bowl-like shape at a depth of approximately 20μm
Equipment utilization example ③: Liquid element concentration measurement
Case 1: Analysis on concentration of nickel chloride (NiCl2・6H2O) was carried out using a potential difference automatic titrator.
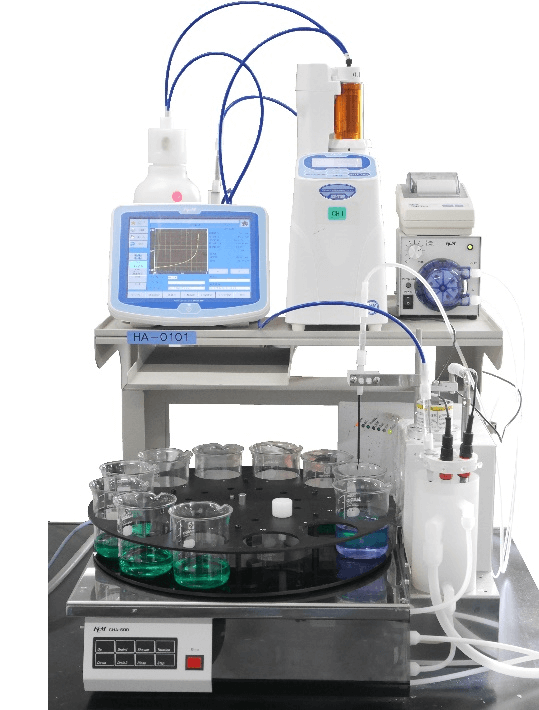
Nickel chloride was added to the Ni-plating bath with the purpose of improving bath electric conductivity and anodic dissolution.
If it exceeds the control value range, it will become impossible to meet the properties require of plating deposition, reducing smoothness and increasing internal stress due to the rise in film hardness. Monitoring this through periodic analysis decreases variations and maintains great plating properties.
Case 2: Plating film and anode impurity analysis
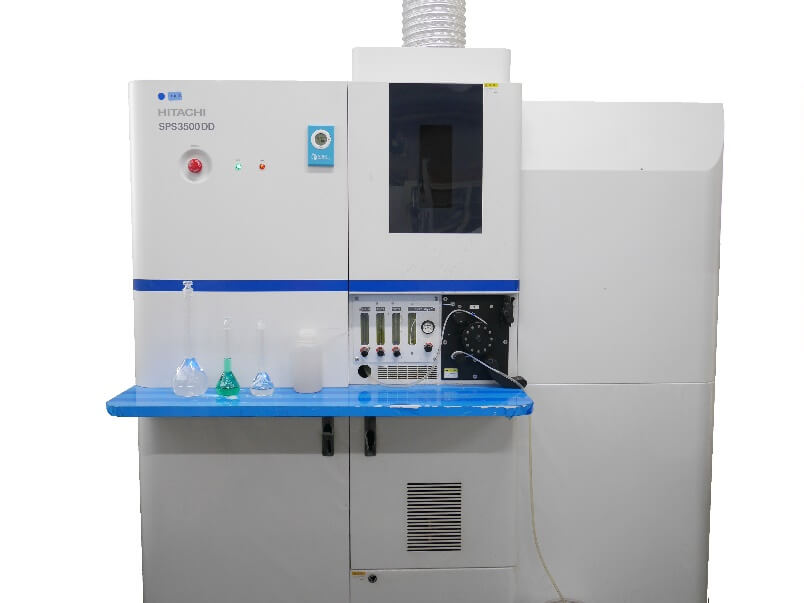
ICP atomic emission spectrometry analyzer
When refining tin anode used in tin plating from tin ore, it is difficult to completely remove lead and as it is always considered as an impurity, it is necessary to control the lead threshold level. We use tin anodes with a purity of 99.99% and monitors threshold levels by periodic measurement.